Es ist erstaunlich leise für eine Welt, in der dutzendfach Nähmaschinen rattern, Nieten in dicken Stoff getrieben werden, Dampf die frisch verschlossenen Hosenbeine bläht. Vielleicht liegt das an den hohen Stapeln von Stofflappen, die hier auf kleinen Rollwagen wie Autos auf einem Supermarktparkplatz in Reih und Glied liegen, bereit für die Verarbeitung an der nächsten Station. Vorderseite, Rückseite, Vordertaschen, Potaschen, Innenfutter. Vielleicht liegt es an den Gummimatten, die den Arbeiter:innen an Bügelmaschinen, Knopfloch-Tackern oder am Zuschnitt das Stehen bequemer machen sollen. Vielleicht aber liegt es auch daran, dass feine Vorzeichen der Betriebsferien durch die Fabrik ziehen. „Die Produktivität höre ich am Geräusch“, sagt der Chef dieser Welt und spitzt die Ohren. „Ja, heute liegen wir ein wenig unter dem Schnitt.“ Hans-Uwe Gansfort lächelt. Macht nichts, 1.200 Jeans pro Tag sind es normalerweise, gefertigt in etwa 17 Minuten pro Stück. In Mönchengladbach.
Eine Jeansfabrik am Niederrhein 2023? Wo vor Jahren die traditionelle Textilregion abgewickelt wurde, schnurren wieder Nähmaschinen? Gansfort nickt. Die Globalisierung ist auf Rückwärtskurs, die Produktion kommt zurück ins Land. Und er will zeigen, dass das geht: Massenmode made in Germany. Günstig, nachhaltig, lokal. In der ersten Jeansfabrik von C&A in Deutschland. Das Backsteingemäuer ragt hoch in den kobaltblauen Julihimmel. A. Monforts Maschinenfabrik steht in goldenen Lettern am Giebel. Im 19. Jahrhundert hat hier der Unternehmer August Monforts seine erste „Rauhmaschine für textile Waren mit fünf Walzen“ hergestellt, später wurde die Firma Weltmarktführerin im Bau von Textilmaschinen. Heute ist das „Monforts Quartier“ eine Innovationslandschaft für Tech-Start-ups, Stiftungen und ein Textil-Forschungszentrum der Stadt und der Hochschule Niederrhein.
Halle 35 ist hoch und hell wie eine gotische Kathedrale, der Boden so blau wie die Stoffe, die auf ihrem Weg zur Jeans 40 Stationen durchlaufen, vom Stoffballen bis zum Versandkarton. Auf 3.300 Quadratmetern stehen digital gesteuerte Textil-Cutter, mit Lasern ausgestattete Messstationen, neueste Industrie-Nähmaschinen, an jedem Arbeitsplatz ein Computermonitor – auf den ersten Blick wähnt man sich eher in einer Chip-Fabrik als bei der Hosenherstellung. Wären da nicht die verhedderfrei gespannten Fäden, die von den großen Garnrollen zu den Nähstationen führen, und, natürlich, die jeansblauen Bahnen überall. „Alle zwei Wochen bekommen wir bis zu zehn Tonnen neue Ballen geliefert“, sagt Gansfort. Der Fabrikchef steht unter Druck. 400.000 Jeans im Jahr sollen bald vom Band laufen, 2.000 am Tag, wenn es optimal läuft. Acht Modelle von Flare bis Skinny aus lokaler Produktion für die Kund:innen im Laden, für 59 Euro das Stück. Gansfort: „Das macht uns unabhängig von Lieferketten.“
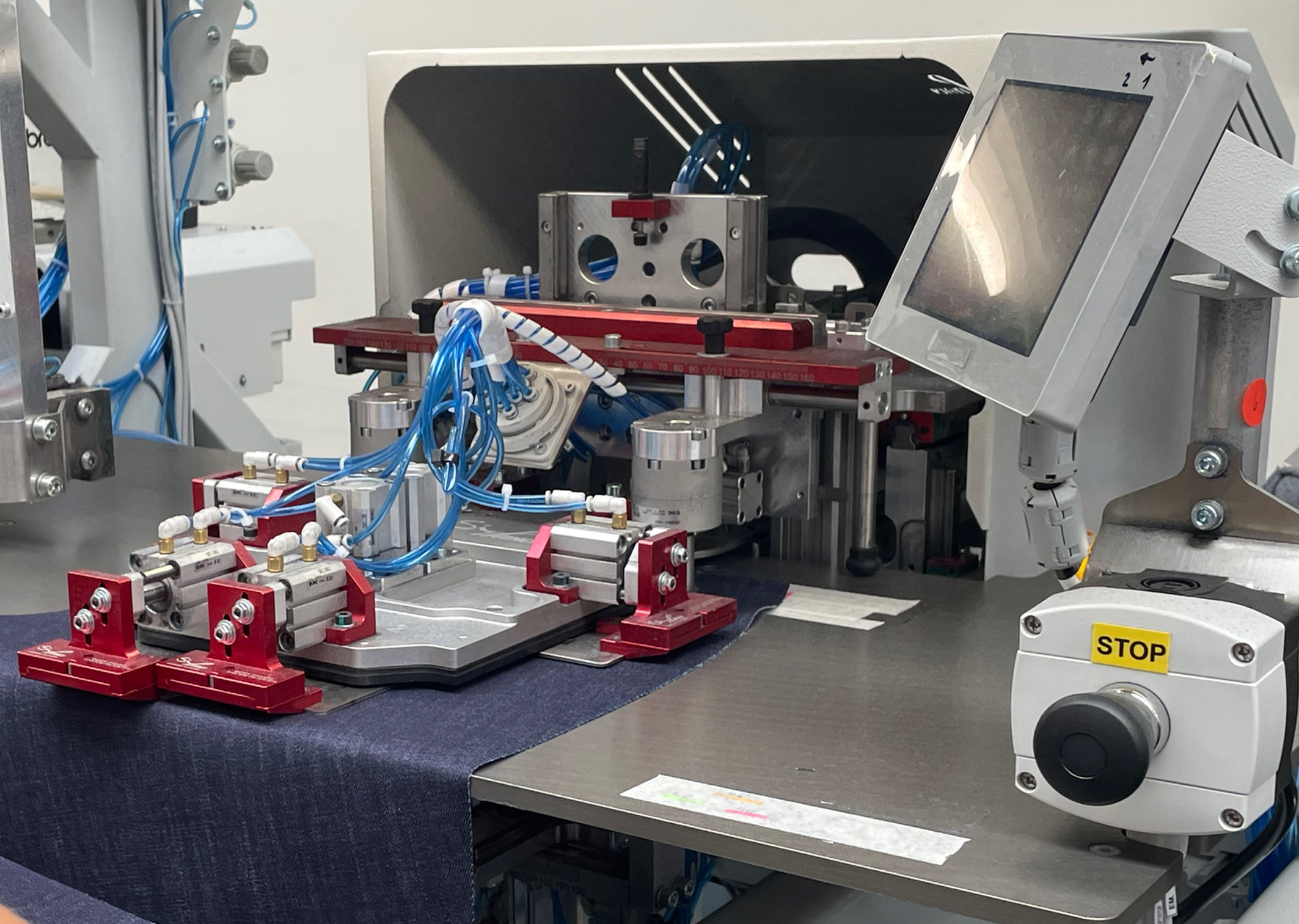
Lokal wird zur Frage der Selbsterhaltung
Denn es ist ungemütlich geworden für die Textilindustrie. „Durch die Corona-Pandemie und den Krieg in der Ukraine hat die Branche gespürt, wie unsicher ihre Lieferketten sind“, sagt Katrin Freier, Professorin für Bekleidungsentwicklung an der Hochschule Niederrhein. In Asien, wo die meisten Textilien produziert werden, sperrten Frachthäfen, Transporte verzögerten sich, Liefertermine platzten. Bei Nike etwa verdoppelten sich zwischenzeitlich die Lieferzeiten, bei H&M war ein Fünftel der weißen Damen-Shirts laut der Analysefirma StyleStage gar nicht mehr lieferbar. „Die Anfälligkeit der Lieferketten kann keiner ignorieren“, so Freier. „Zudem setzen die steigenden Kosten für Transport-Container, Rohstoffe wie Öl oder Baumwolle und für Energie die Kleidungshersteller unter Druck.“ Also schauen sich Modeunternehmen zunehmend nach Alternativen um. „Schon aus Selbsterhaltungsgründen ist es ratsam, die Fertigung näher an Europa zu ziehen oder wenigstens Reservekapazitäten anzulegen“, sagt Arnd Huchzermeier, Professor für Produktionsmanagement an der WHU – Otto Beisheim School of Management in Vallendar. „Mittelständler machen das längst, nun setzen auch die Großen wie Boss oder C&A auf ,De-Risking‘.“ Heißt, sie verlagern zumindest einen Teil der Produktion zurück nach Europa, um weniger krisenanfällig zu sein.
In Mönchengladbach bittet Hans-Uwe Gansfort Platz zu nehmen und schenkt einen Kaffee ein. Sein Büro sieht aus wie ein Berliner Tech-Start-up. Industrieloft, alte Stahlträger, kalkweiße Wände, Glasdach, eine steril-schöne, immer frische Office-Landschaft, die Raum für neue Gedanken lässt. Gansfort, schlank, federnder Gang, wacher Blick, von Kopf bis Fuß in C&A gehüllt, scheint einer, der gern das Neue sucht. Vielleicht gerade weil sein Leben mit C&A so lang und eng verbunden ist, dass er sich kaum noch etwas anderes vorstellen kann.
Noch ein Kaffee und das wars
Mitte der 1980er-Jahre hat er bei C&A Einzelhandelskaufmann gelernt, durchlief die interne Managementausbildung. C&A, das war damals etwas. Guter Ruf, top Ausbildung. Sakkos, Konfektionswaren, Strick, ein Unternehmen mit Tradition und 14 eigenen Fabriken im Land. Irgendwann übernahm Gansfort die Leitung der C&A-eigenen Produktion in Mettingen, dem Geburtsort der C&A-Gründer Clemens & August Brenninkmeijer. „Wir hatten die schnellste Fertigung der Welt: 85 Minuten für ein Sakko.“ Dann bricht der Markt ein. In den 1990ern verliert Qualitätsmode an Stellenwert, Hauptsache billig. Es ist die Zeit von Fast Fashion – und Globalisierung. Fast die gesamte Textilbranche packt ihre Sachen und zieht nach Fernost, wo die Löhne nicht mal ein Zehntel so hoch sind. „Nähmaschinen kann man leicht anderswo aufstellen“, sagt Gansfort. Auch er und seine schnellen Näher:innen sind zu teuer. 78 Pfennig die Lohnminute, schon in Polen kostet sie nur 24 Pfennig. „Da kann man halb so schnell sein und ist trotzdem noch günstiger.“ Anfang der 00er-Jahre ist es so weit: Entlassungen, Sozialpläne, Schluss. An einem Freitag im Dezember 2004 fährt Gansfort als Letzter in Mettingen vom Hof. „Noch einen Kaffee mit Kolleg:innen, Schlüssel umdrehn, das wars“, erinnert er sich. „Bitter.“
Und so hat sich die Wirtschaftsgeschichte der letzten 30 Jahre in Gansforts Karriere ebenso eingeschrieben wie die des Unternehmens. Nach Mettingen organisiert er den Zug gen Osten mit, Einkauf, Technik, Betreuung der Betriebe vor Ort. „Alle waren damals unterwegs, eröffneten Büros, suchten Kooperationspartner.“ Auch sei, die pauschale Kritik ärgert ihn, nicht alles „schmuddelig“ in den Fabriken der Globalisierung gewesen, nicht alles voller Ausbeutung und Low-Tech. Ja, es gebe solche Betriebe – ebenso solche, die es besser machen, damals wie heute. „Wir haben strenge Tests durchgeführt, auf ordentliche Arbeitsbedingungen geachtet und eine Bezahlung, von der man leben kann, Living Wages.“ Doch immer weiter wuchs der Kostendruck, stiegen auch anderswo Löhne, immer schwieriger wurde es, eine günstige Produktion noch irgendwie mit Öko- und Sozialstandards zu vereinbaren. Weiter also gen Osten. Polen, Rumänien, Türkei, Vietnam, China, Bangladesch. „Irgendwann haben wir uns gefragt: Bald sind wir rum um den Globus – und stehen wieder in Deutschland. Und dann?“
Die Frage hat Gansfort nicht mehr losgelassen. Wie kann das gehen: Im Deutschland von 2023 Mode zu machen? Für ihn steht fest: Nachhaltig muss es sein – um die ökobewussten Kund:innen zu überzeugen, die laut Studien immer mehr werden. Hochautomatisiert – um die hohen Lohnkosten abzufedern. Gansfort entwickelt ein Konzept. Bei einem Zoom-Call aus dem Homeoffice im Corona-Mai 2020 überzeugt er das Management. Ein Jahr später startet die C&A „Factory for Innovation in Textiles“ (FIT) in Mönchengladbach.
Hohe Standards beim Arbeitsschutz
Kurz vor Mittag. Stau auf den Ablagetischchen vor der Station, an der die Rückseiten der Hosenbeine verschlossen werden. Anna hat vorgelegt, 1.500 Gesäßtaschen schafft sie pro Tag. Beinrückseite auflegen, Tasche drauf, sekundenschnell zieht die halbautomatische Nähstation ihre Bahn über das Stoffstückchen. Die gelernte Näherin aus Polen liebt „die gute Atmosphäre im Team und die Arbeit an den neuen Maschinen“, in viele hat sie sich schon eingearbeitet. „Ab und zu wechseln ist perfekt.“ Tanja, einst Friseurin, jetzt an der Vordertaschen- und Reißverschluss-Station im Einsatz, setzt lieber auf Routine. „Die Handgriffe hier beherrsche ich im Schlaf.“
Gut 80 Menschen arbeiten in Mönchengladbach. Einige sind Profis wie Anna. Andere haben sich in der zweimonatigen Qualifizierung eingefuchst, die Arbeitsagentur und Textilakademie mit der Hochschule Niederrhein und C&A entwickelt haben. Die Kooperation rettete Gansforts Experiment. „Die richtigen Mitarbeiter:innen zu finden, war die größte Unsicherheit am Projekt.“ Mit der Abwanderung der Branche ging Wissen verloren. Nun findet Gansfort fast alle Mitarbeiter:innen über die Arbeitsagentur. Etwa ein Drittel Männer, zwei Drittel Frauen. Sie kommen aus Osteuropa, dem Iran, Syrien oder Nigeria. Junge Geflüchtete sind dabei und letzte Profis aus der Zeit vor der Globalisierung. Manche haben Erfahrungen in Textilfabriken Pakistans oder der Türkei gesammelt, andere sind Seiteneinsteiger:innen aus der Reinigungsbranche oder Menschen wie Roswita, Kürschnerin aus dem Ort: „Aber wer will heute noch Pelze?“
Der Arbeitsschutz garantiert in Deutschland hohe Standards. Doch Gansfort experimentiert weiter. Hat Steharbeitsplätze eingeführt, weil „Sitzen das neue Rauchen ist“. Will die Geräuschkulisse noch mehr dämmen. Hat gleich einen Termin mit dem Vermieter der Fabrik: Wie lässt sich die Temperatur besser regulieren? „Die einen wollen eine Klimaanlage, die andern möchten sie auf keinen Fall. Gestern waren hier 30 Grad, das ist hart.“ C&A zahlt nach Tarif. Etwa 14 Euro die Stunde gibt es im Schnitt, je nach Qualifikation. Die Lohnkosten sind zehnmal so hoch wie in Bangladesch. Vor allem deshalb kostet die Jeans doppelt so viel wie die Standardware. 59 statt 30 Euro. Die Gewinnmarge ist Firmengeheimnis.
Ohne Automatisierung wird das Deglobalisierungs-Experiment am Niederrhein also nicht laufen. Theoretisch. Praktisch ist viel filigrane Fummelarbeit zu leisten, die keine Maschine schafft. Stoffkanten gegeneinander falten, beim Nähen umklappen, um enge Kurven führen. Das weiche, schwabblige Material kann ein Roboterarm nicht so leicht packen wie den Kotflügel eines Fahrzeugs. Und so steht der Roboter, der die Potaschen, zack, zack, aber leider schief positionierte, heute als Mahnmal technischer Grenzen unter einer Glasvitrine in Halle 35 und Anna übernimmt wieder. Auch Tanjas halbautomatische Sortierhilfe, die fertig zusammengenähte Innen- und Außentaschen flink von der Nähmaschine zieht und in eine Kiste stapelt, ist langsamer als Tanja selbst. Wobei, „die Zusammenarbeit mit den Maschinen ist Übungsfrage, nicht?“ fragt Gansfort und Tanja wiegt lächelnd den Kopf. „Na ja.“
Die Fehlerquote sank von 15 auf 5 Prozent
Zeit für Zahlen: „Anfangs haben wir 300 Jeans am Tag geschafft, heute sind es mehr als dreimal so viele. Und die Fehlerquote ist von 15 auf 5 Prozent gesunken, ist doch was, oder?“ Gansfort weiß, dass es gelingen muss, die Automatisierung zu optimieren. Noch liegt der Break-even in der Ferne. Produktiver werden heißt die Strategie, angesichts des Fachkräftemangels eh unvermeidlich. Gansfort setzt auf die Kooperation mit den Ingenieur:innen von der Textilhochschule Niederrhein und der RWTH Aachen. Ein digitalisiertes Materiallager wird bald getestet. Der digitale Cutter, der für maximal zehn Prozent Abfall beim Verschnitt sorgt, läuft schon rund. Oder die Lasermaschine, die die Maße der fertigen Jeans kontrolliert. Leider ist sie gerade kaputt.
Und wie nachhaltig ist Ihre Fabrik, Herr Gansfort?
Ein Durchgang führt zur Waschhalle. In gewaltigen Trommeln drehen sich Jeans im Wasserbad, statt Chlor wird umweltfreundliches Ozon eingesetzt. Das modulare Filtersystem, ausgetüftelt vom Start-up 140 Fahrenheit, spart Wasser: 10 Liter braucht es nur pro Jeans – statt 60 bis 90 wie sonst. Fünfzig Prozent des Waschwassers wandert in den Kreislauf zurück, sagt der Fabrikchef und führt zur Laserbox. Die Jeansbeine sind breitbeinig aufgespannt, fauchend wird der Used-Look auf den Stoff gelasert. Keine Steine, keine Chemikalien nötig.
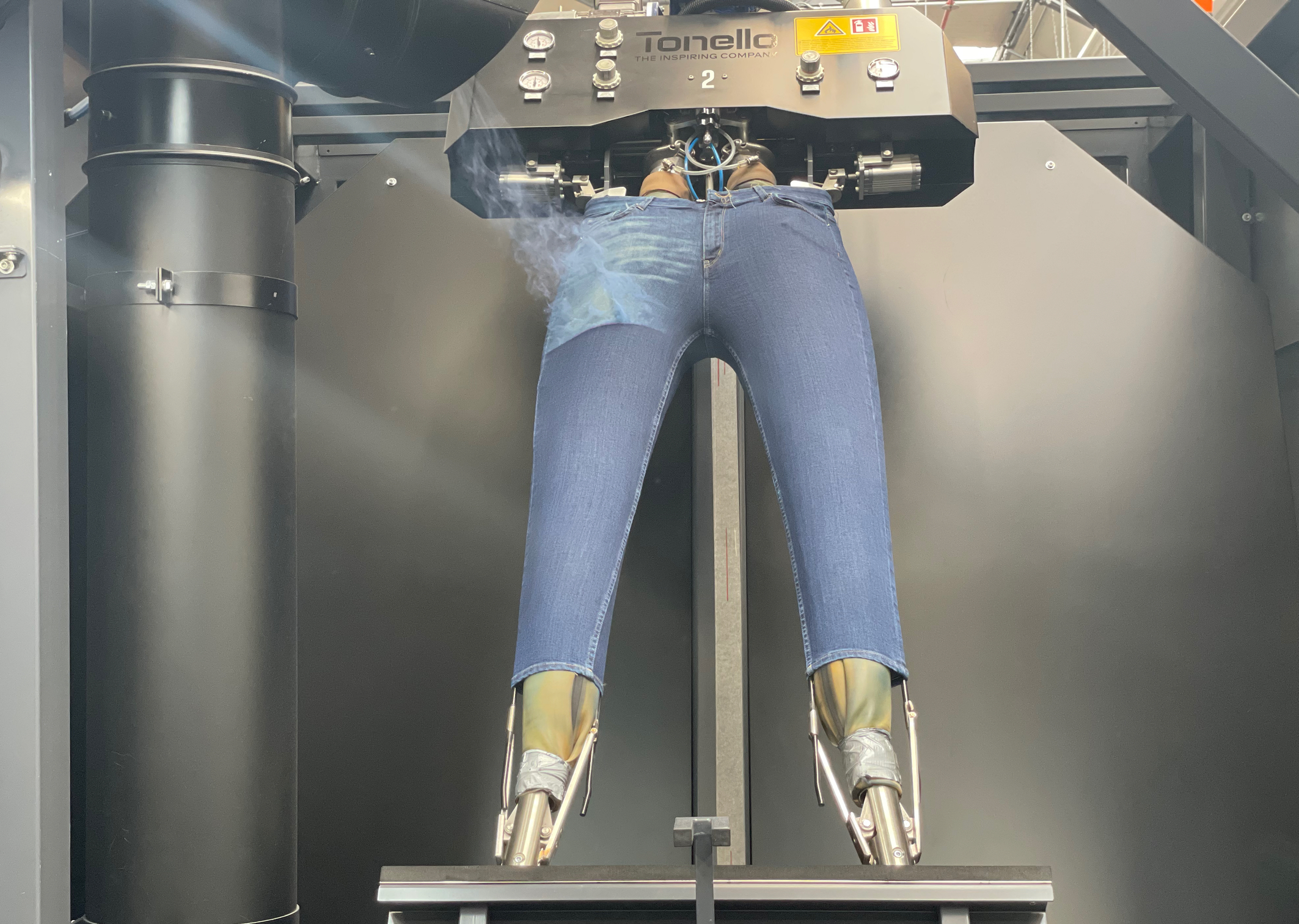
Noch wird der Motor für den Maschinenpark im Mönchengladbacher Deglobalisierungs-Experiment zu 100 Prozent vom Energiepark aus dem nahen Wachendorf angetrieben. Das fuchst Gansfort. Die Energie soll sich mal aus einem Mix von Wind und Solar aus eigener Pr…
Die lokale Produktion sei weniger krisenanfällig und biete hohe Arbeitsschutz-Standards.